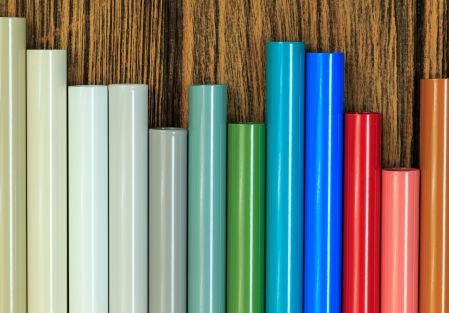
A surface treatment consists of a coating or a process in which a coating is applied to or in the material. There are various surface treatments available for aluminium, each with its own purposes and practical use. As such, the treatments can be used to protect the surface of the material, but also to embellish it or to ensure better adhesion if it requires gluing or painting.
In this blog we will discuss the most common surface treatments for aluminium: sublimation, anodising, powder coating and wet painting.
Sublimation
The sublimation process of aluminum begins with the pre-treatment of the profile. The profile is then pre-painted with a powder coating, giving it a protective and decorative layer. In the second phase, the profile is covered with a sublimation transfer, previously printed with the decorative effect chosen by the customer.
To allow the decoration to be transferred to the profile itself, the latter is placed in an oven at a high temperature: thanks to a combination of heat and pressure, the pigment molecules are dispersed in the form of gas, passing through the pre-printed film support to the paint layer of the profile, definitively transferring to the aluminum.
The last phase is dedicated to the removal of the film and to all the necessary checks to ensure that the decoration has penetrated into the paint on the profile, always guaranteeing high quality.
Comhan can supply aluminium profiles in various wood-effect sublimation finishes. Start combining the benefits of aluminium with the appearance of wood!
Anodising
When anodising aluminium, an electrochemical process is used to form an oxide layer in/on the material. As such, this oxide film forms a protective layer in/on the aluminium. What’s interesting about this, is that no additional layer is applied to the aluminium when anodising. This is because anodising provides a protective layer that is built up from the already existing aluminium. The oxide film is fully integrated into the aluminium, thanks to a strong molecular connection.
The main reason for anodising is to protect the aluminium. Thanks to the anodising process, corrosion resistance increases and the material retains its appearance for longer. The hard, wear-resistant anodising layer that is created protects the underlying aluminium, making it a more durable end product.
The oxide layer can also have great decorative value. Anodisation also makes it possible for aluminium to take on various attractive colours. While the unique metal character of the appearance is retained, it also acquires a nice look. The aluminium is therefore not only better protected, but also embellished.
Want to know more about anodising? Then read our detailed blog about anodising aluminium.
Powder coating
To provide the aluminium with a decorative and protective layer, a powder coating can be opted for. After a number of pre-treatments, which include degreasing and rinsing, the powder coating is applied by means of an electrostatic process. The negatively charged powder is hereby applied to the aluminium object, which is positively charged. The subsequent electrostatic effect creates a temporary adhesion of the coating. The object is then heated in a cure oven so that the coating melts and flows, forming a continuous liquid film. Once it is cured, a solid connection is formed between the coating and the aluminium.
Because, unlike with wet paint, no solvents are used when applying the powder coating, it is also a more environmentally friendly alternative. On the other hand, the end result following powder coating is slightly rougher, as the texture of the granules used remains somewhat visible.
Wet paint
Wet paint is an interesting alternative where aesthetics takes precedence. It produces the best end product, as a much smoother result is achieved. Also, certain decorative effects that are not feasible with powder coating, can be applied to wet paint.
What’s also convenient, is that with this surface treatment there are no maximum dimensions to take into account. This is the case with powder coating, as a spray booth is used. As this is not needed for wet paint, maximum dimensions of the aluminium to be coated don’t require consideration. That is why wet paint is a practical solution for colouring large aluminium parts.
Want to know more? Then read our ‘Aluminium wet paint or powder coating’ blog.
Pre-treatment is essential
Whether you opt for anodising, powder coating or wet paint; the right pre-treatment is always very important. Without the pre-treatment, the anodising layer, powder coating or wet paint may not adhere well to or integrate into the aluminium, causing it to peel off quickly or not be evenly applied.
To ensure optimum adhesion, the aluminium is passed through a spray tunnel, or the material passes through several baths in which it is degreased and stained. A conversion layer is applied in a final bath, which ensures that the best possible adhesion or integration can occur between the aluminium and the anodising layer, paint or coating.
Do you want to know which surface treatment is best for your aluminium product? We’d be happy to tell you more about the choice of anodising, powder coating or wet paint: